Сергей Казанцев, НЛМК: Монополия на «цифру» уходит в прошлое
Металлургия — это довольно консервативная отрасль, однако большую часть производственных процессов уже можно оцифровать. Какой эффект дают новые инструменты, зачем заводы вкладываются в инсорс-разработку промышленного ПО и будут ли производственные компании конкурировать с традиционными ИТ-вендорами, в интервью CNews рассказал вице-президент по цифровизации производства группы НЛМК Сергей Казанцев.
«Команда по цифровизации должна понимать суть производства»
CNews: Считаете ли вы НЛМК цифровой компанией? Почему?
Сергей Казанцев: Да, если исходить из конкретных критериев, которые помогают это оценить.
Первый — это отношение к данным в компании: настроена ли она принимать решения на их основе, сколько инвестирует в источники данных, в измерения, в справочники, в платформы. Мы инвестируем существенно — причем по всей вертикали: от средств измерений до корпоративных хранилищ данных, систем визуализации, анализа и принятия решений. И это поддерживают все: и руководство группы, и специалисты на производстве.
Второй критерий — как цифровая компетенция распределена в компании: какая доля подразделений в ней владеет своей цифровой повесткой, знают ли они, что, как нужно делать, и что это им даст, какой опыт в разработке решений у них есть, и что они могут сделать сами.
Монополия на «цифру» уходит в прошлое. Мы стремимся к тому, чтобы производственные команды осознанно подходили к внедрению цифровых решений, видели в них средство достижения своей бизнес-стратегии и располагали всем для их реализации. Нужно, чтобы они могли сами сформулировать требования с учетом специфики и приоритетов производства, участвовать в выборе и апробировании технологий, встраивать их в процессы. Продукты должны проходить полноценный путь развития, необходимый для достижения эффекта. Для нас важно, чтобы наши пользователи на производстве мыслили не в формате «нам внедрили систему», а «мы сделали систему под наши задачи».
Третий критерий — как цифровые технологии участвуют в реализации стратегических целей компаний. «Цифра» — действительно, важный компонент для реализации стратегии или просто «хайповая» история? «Цифра» — и правда часть дискуссии в компании на уровне руководства?
В НЛМК на сегодняшний момент digital-технологии — неотъемлемая составляющая стратегии как минимум трех направлений: операционная эффективность, охрана труда и работа с клиентами. Без цифровизации цели в этих областях недостижимы.
CNews: Как повысить вовлеченность бизнес-заказчика в цифровизацию? Когда он понимает, что ему нужен конкретный проект, и сам его реализует?
Сергей Казанцев: Мы экспериментировали с форматами «цифровых» команд и поняли, что главный фактор успеха — это вовлечение в процесс ключевых людей из производства с самых первых этапов, то есть с определения того, что, зачем и как делать.
С другой стороны, можно инвестировать в любое ИТ-решение. Но если разработчики не представляют, в каких условиях оно будет работать, за счет чего поможет снизить расход материалов, повысить производительность или качество продукта на конкретном переделе — проект потонет в итерациях и доработках. Просто потому, что предусмотреть в техническом задании все заранее невозможно. Каждый участник процесса должен стремиться ставить себя на место других, с интересом заходить на «чужую территорию» — это касается знаний, целей и подходов к работе.
Мы больше года потратили на то, чтобы наладить правильное взаимодействие в командах, обозначить ценность цифровизации для каждого участника, чтобы все получали удовольствие от наблюдения результатов своей работы. Не только в цифрах и показателях, но и вживую — в «железе».
Сейчас в каждом производственном подразделении, в каждом цехе на Новолипецком металлургическом комбинате, на «Стойленском ГОКе» в Белгородской области у нас появились такие специалисты. Они фокусируются на цифровых технологиях, формируют требования к системам, сопровождают проекты и отслеживают эффективность систем на практике. Чтобы адаптировать решение, нужно физически присутствовать на производстве — с внешней командой это сложно.
CNews: Расскажите о ключевых проектах цифровизации, которые вы реализуете сейчас и планируете запустить в ближайшее время.
Сергей Казанцев: Полтора года назад мы запустили программу «Умное производство», суть которой не столько в проектах и технологиях, сколько в договоренности о том, как мы инвестируем в «цифру» и что за цель формулируем. Мы утвердили цели, подходы, решили, как будем последовательно повышать зрелость автоматизации, и разработали целевую архитектуру производств — «генплан». Важно было понять, что нужно делать уже сейчас, а что — позже. Мы расставляли приоритеты, прогнозируя, как повысит новый процесс операционную эффективность на горизонте года или пяти лет.
Сейчас в основном инвестируем в средства измерения, порядок и визуализацию данных, расчет оптимальных режимов, шихтовок, маршрутов. В нашей терминологии это означает «начальный» и «продвинутый» уровень цифровизации. Анализаторы состава руды и чугуна, плотномеры пульпы на обогащении, лидары для оценки запасов на открытых складах, толщиномеры полосы на прокатке — уже установлены сотни средств измерения, камер с видеоаналитикой, RFID считывателей для слежения за движением материалов по производственной площадке.
Мы накапливаем данные, анализируем, как они связаны друг с другом, и делаем из них модели, базы рецептов, настройки регуляторов. Доводим знания до людей и предоставляем им удобный формат взаимодействия через системы с веб-интерфейсом. Так мы постепенно заходим в зону принятия решений, не останавливаясь на одних измерениях. Причем решения, которые поддерживаются цифровыми ассистентами, учитывают больше факторов и зависимостей «в моменте». Учитывается качество сырья, состояние оборудования, портфель клиентских заказов. Даже опытному эксперту вручную за таким количеством факторов уследить сложно.
Реализуя такие проекты, мы нарабатываем опыт и создаем платформы для перехода на третий, «автономный» уровень. Он связан с изменением роли людей — больше контроля за системами, меньше ручного управления. Появление на производстве специалистов, сопровождающих проекты, о которых мы говорили ранее — один из шагов к этому.
Пример — сервис оптимизации стоимости угольной шихты для производства металлургического кокса. Измерения — это упорядоченные в MES системе данные о характеристиках закупаемых углей и сканируемый лидарами профиль поверхности угольного склада. Модели движения партий углей по складу и процессов коксования позволяют прогнозировать качество производимого металлургического кокса для разных вариантов угольных шихт.
Оптимизатор рекомендует наилучшую шихту под целевые характеристики кокса из располагаемых запасов углей. Показывает исторические характеристики кокса, достигнутые на аналогичной шихте в прошлом. После того, как эксперты-технологи примут итоговое решение, система рассчитывает уставки для дозаторов и передает информацию персоналу на дозирующие устройства.
CNews: Какие еще направления «Умного производства» можно выделить?
Сергей Казанцев: Долгосрочное планирование программы и ее вклада в стратегию позволили эффективнее развивать инфраструктуру. Например, сеть pLTE или новую MES платформу, которую мы реализовали на современном технологическом стеке. Это собственная разработка, хотя некоторые компоненты мы приобрели у партнеров.
Она обеспечивает новый уровень сквозного управления производством продукции, слежения за технологией. Сейчас с любого рабочего места можно следить за работой любого агрегата НЛМК с планшета или ноутбука в реальном времени, смотреть аналитику, план-факт анализ и другие данные. Теперь мы с планшетом в руках проводим гэмбу (это оценка работы системы на том участке, где она должна приносить ценность). Проходим несколько цехов, отслеживая не только продукцию в физическом виде, но и ее цифровой след — характеристики, события, соответствие ключевым параметрам технологических инструкций.
CNews: Расскажите о вашем опыте разворачивания промышленной сети 5G, какие новые возможности получили в результате?
Сергей Казанцев: Да, в части развития инфраструктуры один из ярких проектов — это корпоративная LTE-сеть. Это десятки базовых станций на двух площадках, возможность иметь надежную технологическую связь с движущимися объектами — тепловозами и электровозами, самосвалами, территориально распределенными производствами, датчиками в труднодоступных местах, где нет фиксированной сети.
Подобная инфраструктура формирует базу для будущего развития. Так, сделав MES с удобным веб-интерфейсом, который открывается на любом современном планшете, и сеть pLTE, мы можем раздать персоналу планшеты для поиска и назначения слябов на складе в прокатку. Отдельно подобные проекты плохо окупаются, если в их бюджет нужно заложить организацию промышленного WiFi и разработку пользовательских сервисов «с нуля». Мы же получили эти возможности условно «бесплатно», по цене самих планшетов.
Также из «быстрых» эффектов — больше возможностей по диагностике оборудования. Мы снимаем телеметрию с кранов в режиме онлайн, что важно для оценки состояния оборудования и мониторинга рисков.
«Российские ИТ-компании оказались не готовы к потоку клиентов»
CNews: Сегодня многие промышленные гиганты ведут инсорс-разработку решений, которые потом предлагают рынку, составляя конкуренцию традиционным ИТ-компаниям. Как вы относитесь к этой тенденции?
Сергей Казанцев: Нужно понимать, что мы этим занимаемся не от хорошей жизни и не для того, чтобы конкурировать с ИТ-компаниями. Мы были бы рады, если бы на рынке было много партнеров с хорошими готовыми решениями, которые можно развивать под потребности нашего бизнеса. И тем более, если бы они также предоставляли оперативную и качественную поддержку.
На практике же часто сталкиваемся с тем, что готовых решений нет, и вендорам приходится перенимать основную экспертизу о процессах у наших же специалистов из производства и технических служб. В случае локальных или не очень сложных решений это приемлемо, но для сквозных или требующих большого погружения в технологию — нет. Нам проще самим нарастить ресурс разработки и выстроить процессы взаимодействия внутри компании.
Мы становимся более продвинутыми в микросервисной разработке и развиваем собственные корпоративные платформы DevOps, MLOps, IIoT, библиотеку совместно используемых сервисов и компонент. И ждем выполнения тех же требований от партнеров, участвующих в разработке — что для менее продвинутых из них может быть «накладно». Для нас же решения, внедренные вне нашей цифровой «экосистемы», усложняют эксплуатацию, их работоспособность и развитие сильно зависят от вендора или отдельных команд.
И третий фактор — не все российские вендоры способны адаптировать свои решения под нас в ходе проектов и выдержать наш темп развития решений. Бэклог развития растет быстрее, чем партнеры успевают проанализировать и реализовать все наши требования. Мы же стремимся быть более адаптивными к рынку, быстрее учитывать изменения в технологиях и внедрять мероприятия по оптимизации, значительная часть которых сейчас включает модификацию прикладных систем.
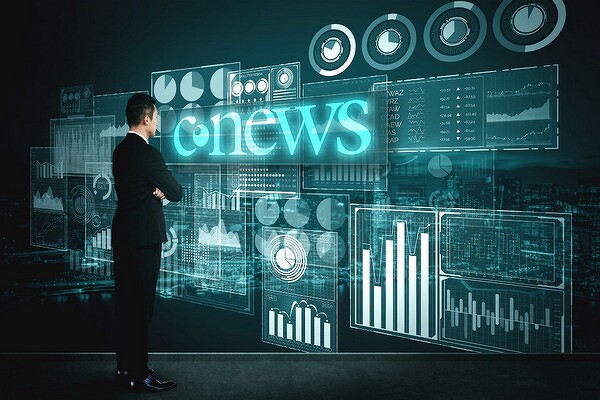
Вот, как мы сейчас работаем: когда мы строим системы, у нас нет цели все написать самим — это и поддерживать накладно, и эксплуатировать сложно. Мы — не ИТ-компания, это не наш бизнес, и потому в любом проекте у нас есть компоненты вендоров, где-то — больше, где-то — меньше. С некоторыми из них мы договорились, что будем сами дорабатывать «фичи» и передавать им их в виде исходного кода, чтобы партнеры интегрировали изменения в ядро и возвращали нам уже в последующих обновлениях. Так дело идет гораздо быстрее. Иначе на это уходили бы годы — допресурс, допзатраты, допконтроль качества и лишнее общение с вендором.
CNews: А в целом как вы оцениваете доступность российских технологий?
Сергей Казанцев: Думаю, со временем все стабилизируется, но сейчас есть ощущение, что часть российских ИТ-компаний оказались немного не готовы к возросшему потоку клиентов и задач. Кажется, что они заняли выжидательную позицию и не слишком активно наращивают ресурсы. У части российских вендоров в целом не было зрелой и устоявшейся модели работы — как сделать продукт из заказной разработки, выстроить лицензионную политику, ценообразование, поддержку. Сейчас они экспериментируют, порой кидаясь из крайности в крайность. К этому добавляется ажиотаж на рынке труда.
CNews: Нишевые решения на рынке тоже найти сложно.
Сергей Казанцев: Да, к примеру, мы сделали систему, важную для нас, для распознавания качества лома черных металлов при приемке. Она позволила сделать приемку более объективной и улучшить условия труда для специалистов. Система базируется на нейросети, и понадобилось расширить нашу платформу MLOps под CV и увеличить команду экспертов по машинному зрению, которые следят за работой системы.
Мы были бы рады вместо этого внедрить готовое решение на рынке, была бы «коробка» — купили бы. Эксплуатация такого решения «в одиночку» обходится недешево, не говоря о его развитии. Нашей системой заинтересовалось несколько компаний-интеграторов и, если они смогут довести ее до состояния продукта, внедрять другим металлургическим компаниям, это было бы выгодно всем.
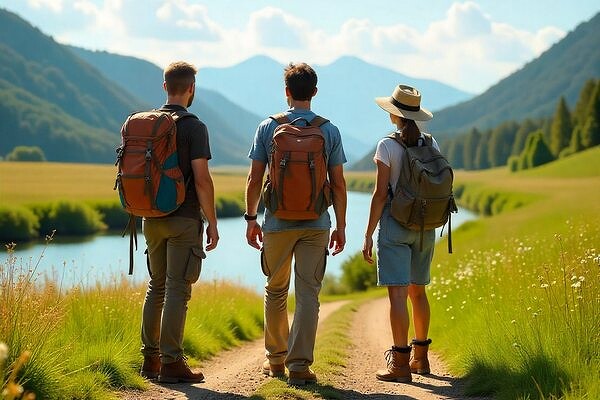
Для интеграторов это основной профильный бизнес, компании-клиенты пользовались бы отлаженным решением, уже обученным на общей базе изображений. А мы бы получали регулярные обновления и сэкономили на эксплуатации. Вдолгую, возможно, и на рынке ломозаготовки формировались бы более прозрачные стандарты качества и процессов приемки, уменьшилась бы доля комиссионной приемки, которая требует личного участия представителей поставщиков и покупателей.
CNews: Получается, это полезно для рынка в целом, ведь интеграторам трудно, они остались без иностранных вендоров. И, наверное, это не первый случай, когда промышленная компания передает интегратору свое решение и помогает ему развиваться как вендору.
Сергей Казанцев: Да, может, в этом и есть выход из странной ситуации, когда потребители софта конкурируют с его производителями, которые вроде бы вдолгую должны этот рынок развивать, ведь это их основной бизнес. Так или иначе, мы сильно заинтересованы в развитии российских ИТ-компаний и конкуренции на рынке. Возможно, лучшие решения и наработки промышленных компаний просто будут «кочевать» к интеграторам и вендорам и в итоге со временем станут частью каких-то отраслевых продуктов.
«В промышленных компаниях будет расти доля ИТ-специалистов»
CNews: Какие новые технологии, на ваш взгляд, выстрелят в ближайшие 3—5 лет?
Сергей Казанцев: Металлургия — это консервативная отрасль, видимо в силу относительного постоянства самой производственной цепочки, длительного жизненного цикла основного оборудования, технологий добычи и обогащения, обработки металла. К примеру, если мы изначально не предусмотрели пространство для линии автоматической подачи цинк-алюминиевых слитков в ванну оцинкования, то мы не будем перестраивать цех, чтобы полностью автоматизировать этот процесс.
В этом смысле сложно представить себе цифровые технологии, которые «выстрелят», то есть кардинально изменят производственную цепочку, на горизонте следующих 3—5 лет.
Когда мы закладываем линейку автоматизации, которая отвечает, например, за правильную кристаллизацию сляба из жидкой стали в машине непрерывной разливки — мы должны рассчитывать на десятки лет ее бесперебойной работы.
Еще на этапе инжиниринга важно закладывать все необходимые «фичи» на перспективу. Если хотим «умный» склад без человека, его именно так и нужно проектировать, с продуманной пространственной компоновкой и технологией транспортировки, обеспечивающей надежное слежение и перемещение продукции в автономном режиме. Если пытаться сделать «умным» склад, построенный, скажем, 20 лет назад с расчетом на ручное управление, в системе неизбежно будут накапливаться ошибки, требующие ручного контроля и вмешательства.
CNews: Ритейлеры говорят, что технологии «умного» склада слишком дорогие, «экономика не сходится». А для вас это перспективно?
Сергей Казанцев: Экономика есть. «Умный склад» слябов позволит быстрее подбирать их для загрузки в нагревательные печи и последующей прокатки, точнее исполнять план на смену. Оптимизировать время от разливки стали до проката, чтобы экономить на энергоресурсах при разогреве перед прокаткой, выполнять меньше крановых операций.
Этих расчетов может не хватать для обоснования всех инвестиций, в организацию полностью автономного склада, но есть возможность двигаться поэтапно. Первым шагом может стать качественная разметка в системе и переход на обмен заданиями между сотрудниками склада, крановщиками через единую систему. Или цифровой ассистент по подбору слябов под текущий график прокатки. Это требует минимальных инвестиций, но значительных организационных усилий. Получив опыт и реалистично оценив, на какой эффект рассчитывать, можно двигаться дальше — отработать систему позиционирования и диагностики кранов, систему маркировки и слежения за слябами. Мы примерно так и действуем.
Также важно понимать, что любой склад — это довольно опасный участок. Чем меньше персонал будет находиться в пространстве движения погрузчиков или кранов, вблизи раскаленных слябов, тем меньше рисков получить травму. Для нас это важный приоритет, не связанный с экономикой. Мы стремимся к тому, чтобы сотрудники основную часть времени следили за «умной» системой с комфортного и безопасного рабочего места.
CNews: Каких ключевых изменений в течение 3–5 лет вы ожидаете в компании?
Сергей Казанцев: Основные изменения на этом горизонте я связываю больше не с применяемыми технологиями, а с подходами к целеполаганию, реализации систем, совместной работе и эволюции ландшафта компетенций.
Существенно вырастет доля инженеров в компании и цифровая грамотность. Значительная часть мероприятий по повышению операционной эффективности будет связана с развитием или созданием цифровых систем, а их поиск и оценка — с продвинутым анализом данных и моделированием.
Компетенции по работе с данными и моделированием станут стандартным инструментом специалистов по развитию основной технологии. Организационно упростится объединение в кросс-функциональные команды, включающие производственную, цифровую, научную экспертизу для решения приоритетных задач. Одновременно с усложнением ИТ-ландшафта из-за разнообразия цифровых инструментов вырастет роль корпоративных платформ и конвейеров разработки и моделирования.
Единая цифровая платформа, над которой мы начали работать три года назад, теперь позволяет делать современный стек решений, постоянно обновлять его и идти в ногу со временем, развивая тот же MES. С одной стороны, у нас большой штат собственных разработчиков, с другой, используем и аутстаффинг, что позволяет быстро масштабироваться, когда нужен рывок, и оптимизироваться, когда необходимо экономнее использовать ресурсы.
CNews: А как меняются требования к инженерам?
Сергей Казанцев: На металлургическом заводе всегда была серьезная инженерная экспертиза. Есть специалисты, которые разбираются в физике и химии процессов, как оптимально организовать буровзрывные работы в карьере, измельчить и обогатить руду, выплавить чугун в доменной печи, сделать из него сталь и прокат. Другие проектируют новые агрегаты — в том числе, у нас есть собственный проектный институт. Третьи занимаются автоматизацией работы этих машин. Отдельные команды отвечают за моделирование и data-science, машинное зрение, микросервисы, развитие сетевой и серверной инфраструктуры.
Мы стараемся создать такие условия, чтобы у них была возможность и интерес работать вместе. Ведь действительно сложные задачи решаются только в команде, необходимо вовлечение большинства этих специалистов. А это требует расширения эрудиции, развития профиля T-shape (T-shaped специалист — это человек, который является экспертом как минимум в одной области, но при этом разбирается во многих других). Особенно когда появляются новые специализации и форматы работы. Можно оставаться узким специалистом в сильно востребованной области, но это может ограничивать и личную эффективность, и потенциал роста сотрудника в компании.
Системы и платформы — это правильно, но системы не создают системы, а платформы не разрабатывают платформы. По крайней мере, пока. Именно люди обеспечивают преемственность знаний и подходов, люди созидают. Поэтому, вкладывая в развитие экспертизы и создание условий для командной работы, мы создаем долгосрочную базу для будущего развития и роста.