Томские ученые улучшили титановые сплавы для биомедицины с помощью 3D-технологий
Ученые ТПУ совместно с российскими и зарубежными коллегами разработали технологию, которая позволяет улучшить биомеханические характеристики титановых сплавов, изготовленных методом электронно-лучевой 3D-печати. В перспективе полученные материалы можно использовать для создания персональных костных имплантатов, обеспечивая более длительный срок их службы и повышая качество жизни пациентов. Об этом CNews сообщили представители ТПУ.
Результаты исследований опубликованы в журнале Materials Science and Engineering A (Q1, IF: 7,0). Работа ученых поддержана грантом РНФ (№ 20-73-10223).
В современной медицине особое внимание уделяется разработке инновационных материалов с оптимальными биосовместимыми характеристиками. В качестве перспективных кандидатов для производства различного рода медицинских имплантатов рассматриваются бета-титановые сплавы с добавлением ниобия, циркония, молибдена, тантала или олова. Данные сплавы имеют преимущественно стабильную кристаллическую решетку бета-фазы, обладают низкой токсичностью, высокой прочностью, хорошо формуются и надежно сплавляются. Однако их модуль упругости, хоть и ниже, чем у коммерчески чистого титана, все еще остается значительно выше, чем у натуральной кости.
«Различие в механических характеристиках создает сложности при интеграции таких титановых сплавов в медицинскую практику. Например, имплантат из такого материала может принимать на себя основную нагрузку, в то время как окружающая его костная ткань начнет деградировать. Поэтому появляется необходимость в приближении упругости искусственного материала к упругости костной ткани», — сказала соавтор исследования, руководитель научной группы «Аддитивные технологии получения и исследования перспективных материалов» ТПУ Ирина Грубова.
В ходе исследования ученые методом электронно-лучевой 3D-печати в различных режимах изготовили образцы сплава из порошка титана с содержанием массовой доли ниобия 56%. Выбор режимов был сделан на основе ранее полученных данных окна параметров для близкого по составу сплава титана с содержанием массовой доли ниобия в 42%.
«Для получения исходного материала мы сначала сплавили титан и ниобий, а затем получили из него порошок для дальнейших исследований. Это решило проблему неоднородности, которая возникала ранее при использовании элементарных порошков из-за различных температур плавления титана и ниобия», — отметила Ирина Грубова.
В процессе получения материала были применены три различных набора технологических параметров. Основное отличие между образцами заключалось в интенсивности тока пучка при печати, что позволило детально изучить влияние этого фактора на микроструктуру и свойства полученного сплава.
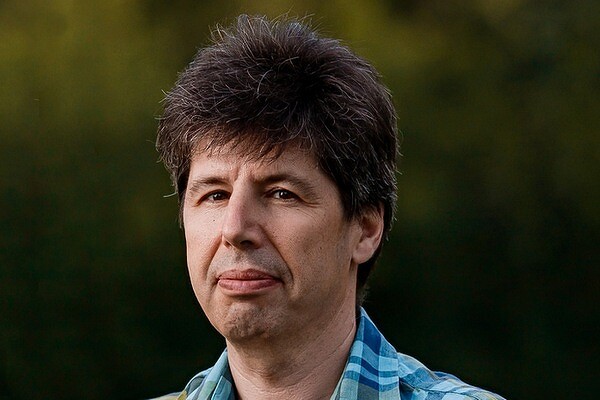
Исследования показали, что более низкая энергия усиливала стабилизацию кристаллической решетки. Механические испытания на сжатие определили, что использование тока 4 мА позволяет достичь наивысшего предела текучести, благоприятного расположения атомов внутри сплава, сниженного модуля упругости и повышенной износостойкости.
«Полученные результаты свидетельствуют о том, что, изменяя только параметры печати, можно управлять внутренней структурой и свойствами сплава. При этом химический состав материала остается неизменным. Это важный шаг в направлении создания индивидуализированных имплантатов с заданными характеристиками», — сказала Ирина Грубова.
В настоящее время ученые продолжают работу над оптимизацией параметров и стратегий печати для изучаемых составов сплавов. Это позволит получить материалы для более широких клинических применений.
В исследованиях принимали участие сотрудники Научно-исследовательского центра «Физическое материаловедение и композитные материалы» и Международного научно-исследовательского центра «Пьезо- и магнитоэлектрические материалы» Исследовательской школы химических и биомедицинских технологий ТПУ, НИИ нанотехнологий и наноматериалов ТГУ им. Г.Р. Державина, МГУ, Института физики металлов им. М.Н. Михеева УрО РАН, Средне-Шведского университета.